A Beginner’s Guide to ISO 9001
A Beginner’s Guide to ISO 9001
Have you ever wondered how businesses consistently deliver high-quality products and services, build customer trust, and improve efficiency? The answer often lies in following a structured system, and that’s where ISO 9001 comes in. This internationally recognized standard for quality management is the foundation of many successful businesses—and understanding it starts with the right ISO 9001 Guide.
Whether you’re a small business owner, part of a growing team, or simply curious about how ISO 9001 works, this guide is here to help. We’ll break down what ISO 9001 is, why it matters, and how you can use its principles to improve your organization. By the end, you’ll have a solid understanding of the ISO 9001 Guide and be ready to take the first step toward implementing this game-changing standard in your business.
Let’s dive in and explore how mastering ISO 9001 can transform the way you work and set you on the path to long-term success!
What is ISO 9001?
Let’s start with the basics: what exactly is ISO 9001? Think of it as a guidebook for running a business that consistently delivers quality. At its core, ISO 9001 is an international standard for quality management systems (QMS). It’s designed to help businesses improve their processes, meet customer expectations, and ensure that everything runs smoothly.
In this ISO 9001 Guide, we’ll break it down so it’s easy to understand. ISO 9001 isn’t just for big companies or manufacturers—it’s for any organization, big or small, that wants to focus on quality. Whether you’re a tech startup, a healthcare provider, or even a family-owned bakery, ISO 9001 provides a framework that helps you work smarter, not harder.
Why Was ISO 9001 Created?
The purpose of ISO 9001 is simple: to create a global standard that businesses can follow to ensure quality. Before standards like ISO 9001 existed, businesses often relied on inconsistent or informal processes, which made it hard to guarantee results. ISO 9001 solved that problem by providing a clear structure for managing quality in a way that works across industries.
Who Uses ISO 9001?
This might surprise you, but ISO 9001 is used by businesses and organizations in over 170 countries! It’s one of the most popular standards in the world, and for good reason. The beauty of ISO 9001 is that it’s flexible—it doesn’t matter what industry you’re in or how big your company is. The principles of this ISO 9001 Guide can be adapted to fit your specific needs.
For example:
- A small e-commerce store can use ISO 9001 to improve customer satisfaction and streamline order processing.
- A large manufacturing company might focus on reducing defects and improving production efficiency.
- Even a nonprofit organization can use ISO 9001 to ensure their programs are delivered effectively.
What Does ISO 9001 Cover?
ISO 9001 is all about creating a reliable quality management system. This ISO 9001 Guide focuses on several key areas, including:
- Customer Satisfaction: Understanding and meeting customer needs is at the heart of ISO 9001.
- Leadership Commitment: Strong leadership ensures quality is a priority throughout the organization.
- Risk Management: Identifying and addressing risks helps prevent problems before they happen.
- Continuous Improvement: ISO 9001 encourages businesses to always look for ways to get better.
Understanding these basics is the first step in mastering ISO 9001. In the next section of our ISO 9001 Guide, we’ll dive into why this standard is so important and how it can benefit your business. Let’s keep going!
Why ISO 9001 is Important
Now that we know what ISO 9001 is, let’s talk about why it’s such a big deal. Whether you’re new to quality management or looking to take your business to the next level, this ISO 9001 Guide will show you why implementing this standard can be a game-changer. Spoiler: it’s not just about compliance—it’s about transforming the way your business operates.
1. Improves Customer Satisfaction
Let’s face it—happy customers are the backbone of any successful business. ISO 9001 puts customer satisfaction front and center. By focusing on understanding and meeting customer needs, businesses that follow this ISO 9001 Guide are more likely to keep their clients coming back for more.
For example, imagine running a tech support company. With ISO 9001, you’ll have systems in place to track client feedback, address complaints quickly, and continuously improve your services. The result? Satisfied customers who trust your brand and spread the word about your reliability.
2. Boosts Efficiency and Reduces Costs
One of the biggest benefits of implementing the ISO 9001 Guide is that it helps you streamline your processes. By analyzing your workflows, identifying inefficiencies, and standardizing procedures, you’ll save time and money while improving overall performance.
For instance, let’s say you’re in the manufacturing business. ISO 9001 can help you reduce production errors by ensuring every step of the process is clearly defined and consistently followed. Fewer mistakes mean less wasted material, fewer delays, and lower costs—all of which add up to a healthier bottom line.
3. Builds Credibility and Trust
In today’s competitive market, trust is everything. Customers and partners want to know they’re working with a business that takes quality seriously. By following the ISO 9001 Guide, you demonstrate your commitment to excellence, which can give you a major edge over competitors.
Think about it: if you’re deciding between two companies and only one is ISO 9001 certified, which one are you more likely to trust? Certification isn’t just a piece of paper—it’s a signal to the world that your business meets globally recognized standards.
4. Supports Continuous Improvement
ISO 9001 isn’t a “set it and forget it” standard—it’s built around the idea of continuous improvement. Businesses that follow this ISO 9001 Guide are always looking for ways to evolve, whether it’s by adopting new technologies, improving customer experiences, or refining internal processes.
For example, a logistics company might use ISO 9001 to analyze delivery times and find ways to make shipments faster and more reliable. Over time, these small improvements add up, keeping the company competitive and ahead of industry trends.
5. Opens Doors to New Opportunities
Many industries and organizations require ISO 9001 certification to even consider working with you. Following this ISO 9001 Guide can open doors to new markets, bigger contracts, and more prestigious clients.
For instance, government contracts or partnerships with global companies often list ISO 9001 certification as a must-have. By achieving it, you position your business as a trustworthy and professional partner, ready to handle large-scale projects with ease.
Why It All Matters
When you break it down, ISO 9001 isn’t just about meeting standards—it’s about transforming your business into a well-oiled machine that consistently delivers value. From happier customers to streamlined operations and greater market opportunities, this ISO 9001 Guide shows how this standard can truly elevate your organization.
In the next section, we’ll dive into the core principles of ISO 9001, giving you a deeper understanding of what drives this powerful standard. Ready to dig in? Let’s go!
The Key Principles of ISO 9001
Now that we’ve explored why ISO 9001 is so important, let’s take a closer look at the foundation of this standard: its core principles. These are the guiding ideas that shape how businesses implement ISO 9001 and why it works so effectively. In this part of our ISO 9001 Guide, we’ll break down these principles in simple terms so you can see how they apply to your business.
1. Customer Focus
At the heart of ISO 9001 is one key idea: customers come first. Every process, decision, and improvement made under ISO 9001 is designed to ensure that customers’ needs are met or exceeded. This principle drives customer satisfaction and helps build long-term loyalty.
How It Works:
Imagine you’re running an online clothing store. By implementing the ISO 9001 Guide, you can create systems to track customer feedback, quickly address complaints, and improve your products based on what customers value most. Satisfied customers are more likely to return and recommend your business to others.
2. Leadership Commitment
Strong leadership is essential for the success of any quality management system. ISO 9001 emphasizes the role of leaders in setting clear goals, fostering a culture of quality, and ensuring everyone in the organization understands their role in meeting those goals.
How It Works:
Let’s say you’re managing a construction company. Following the ISO 9001 Guide, your leadership team would actively engage in setting quality standards, monitoring progress, and motivating employees to prioritize excellence on every project.
3. Engagement of People
No system works without the people behind it. ISO 9001 encourages businesses to engage their employees, giving them the tools, training, and support needed to succeed. When your team feels empowered, they’re more likely to contribute to the organization’s goals.
How It Works:
For example, a restaurant could use the ISO 9001 Guide to train staff on food safety standards and customer service practices. By involving employees in the process, the restaurant ensures everyone is working toward delivering a consistent, high-quality experience.
4. Process Approach
ISO 9001 encourages businesses to think of their operations as a series of interconnected processes. By understanding how these processes work together, you can identify areas for improvement and ensure consistency across the board.
How It Works:
A printing company might use the ISO 9001 Guide to map out their workflow—from taking customer orders to delivering the final product. This helps them identify bottlenecks, reduce errors, and deliver jobs on time.
5. Continuous Improvement
ISO 9001 isn’t about setting up a system and leaving it alone—it’s about constantly looking for ways to improve. Whether it’s through better technology, more efficient processes, or enhanced customer experiences, the goal is to evolve and adapt over time.
How It Works:
A software company could use the ISO 9001 Guide to regularly review their development processes, ensuring they’re always staying ahead of customer needs and industry trends. Over time, this focus on improvement keeps the business competitive.
6. Evidence-Based Decision Making
ISO 9001 emphasizes the importance of making decisions based on data, not guesswork. By tracking and analyzing key performance indicators, businesses can make informed decisions that drive success.
How It Works:
Imagine you run a logistics company. Using the ISO 9001 Guide, you might track delivery times and customer satisfaction rates. If the data shows a consistent delay in one route, you can address the issue and improve performance.
7. Relationship Management
Finally, ISO 9001 highlights the value of strong relationships with stakeholders, including customers, suppliers, and employees. By fostering collaboration and trust, businesses can create partnerships that support long-term success.
How It Works:
For a manufacturing company, this might mean working closely with suppliers to ensure materials meet quality standards. Following the ISO 9001 Guide, these partnerships ensure the final product is reliable and consistent.
Why These Principles Matter
These principles are what make ISO 9001 so effective. By focusing on customers, empowering employees, improving processes, and making data-driven decisions, businesses can create a quality management system that delivers real results.
In the next section of our ISO 9001 Guide, we’ll look at the structure of ISO 9001 and how its different components work together to support your business. Let’s keep building on this foundation!
The Structure of ISO 9001
Now that we’ve covered the key principles, let’s take a closer look at how ISO 9001 is structured. Understanding its layout will help you see how all the pieces fit together and make it easier to implement. In this section of our ISO 9001 Guide, we’ll break down the standard into its main components so you can approach it with confidence.
ISO 9001 is organized into a set of clauses, each focusing on a specific area of quality management. Think of it as a roadmap that guides you through building a solid and effective quality management system (QMS).
1. Context of the Organization
The first step in the ISO 9001 Guide is understanding your organization’s unique context. This means defining your goals, identifying stakeholders (like customers, suppliers, and employees), and recognizing any external or internal factors that might affect your ability to meet those goals.
How It Works:
For example, a small consulting firm might identify its key stakeholders as clients, team members, and industry regulators. Understanding this context helps the firm align its processes with the needs and expectations of these groups.
2. Leadership
Leadership is a cornerstone of ISO 9001, and it’s all about ensuring that top management is fully committed to quality. This clause focuses on setting clear goals, creating a culture of quality, and assigning responsibilities throughout the organization.
How It Works:
Imagine a retail business where the management team leads by example, regularly reviewing quality goals and ensuring employees understand their roles. By following this part of the ISO 9001 Guide, the business can create a strong foundation for success.
3. Planning
Planning in ISO 9001 is all about identifying risks and opportunities. By thinking ahead and addressing potential challenges, you can build a QMS that’s prepared for anything. This section also involves setting measurable objectives to track progress.
How It Works:
For instance, a catering company might use the ISO 9001 Guide to identify risks like late deliveries from suppliers and plan solutions, such as working with backup vendors. Setting clear goals, like reducing delivery delays by 20%, helps the business stay focused.
4. Support
This clause focuses on providing the resources, tools, and training your team needs to succeed. It also covers communication and maintaining accurate documentation to support your QMS.
How It Works:
Let’s say you’re running a digital marketing agency. By following this section of the ISO 9001 Guide, you’d ensure your team has access to the latest software, proper training on new strategies, and a system for tracking project data.
5. Operation
This is the action phase of ISO 9001—it’s all about delivering quality. It involves planning and controlling processes, managing customer orders, and ensuring that the final product or service meets expectations.
How It Works:
A custom furniture maker might use the ISO 9001 Guide to create a step-by-step process for handling customer orders, from initial design to delivery. By standardizing operations, they ensure every customer gets a high-quality product.
6. Performance Evaluation
Once your QMS is up and running, you need to monitor its effectiveness. This clause focuses on measuring results, conducting internal audits, and analyzing data to ensure you’re meeting your goals.
How It Works:
For a logistics company, this might involve tracking delivery times and customer satisfaction scores. By using the ISO 9001 Guide to evaluate performance, the company can identify areas for improvement and take action.
7. Improvement
Finally, ISO 9001 emphasizes the importance of continuous improvement. This clause encourages you to identify opportunities for growth and take corrective action when things don’t go as planned.
How It Works:
A software company could use customer feedback to refine its development process, releasing updates that address user concerns. The ISO 9001 Guide helps ensure these improvements are systematic and sustainable.
How the Structure Helps You Succeed
The structure of ISO 9001 is designed to guide you through every aspect of quality management, from planning to execution to evaluation. By following this roadmap, you can build a system that works for your business, no matter your industry or size.
In the next section of our ISO 9001 Guide, we’ll walk through the steps to implement this structure in your organization. Ready to turn these concepts into action? Let’s get started!
Steps to Implement ISO 9001
Now that we’ve covered the structure of ISO 9001, let’s get into the nitty-gritty of how to actually put it into practice. In this part of our ISO 9001 Guide, I’ll walk you through the steps to implement the standard in your organization. Don’t worry—it’s not as overwhelming as it sounds when you take it one step at a time.
1. Understand the Requirements
The first step in implementing ISO 9001 is getting familiar with the standard’s requirements. This means reviewing the clauses we discussed earlier and understanding how they apply to your business.
How It Works:
Take some time to study the standard, focusing on how each section aligns with your current processes. If you’re new to ISO 9001, consider getting help from a consultant or using guides like this one to simplify the learning curve.
2. Conduct a Gap Analysis
Before diving in, you need to know where you stand. A gap analysis helps you compare your current operations with ISO 9001 requirements and identify areas for improvement.
How It Works:
For example, if you’re running a customer service team, you might discover that while you’re great at resolving issues, you’re not documenting customer complaints consistently. This insight helps you focus on closing that gap as part of your implementation plan.
3. Develop a Quality Management System (QMS)
Your QMS is the backbone of ISO 9001. It’s a set of documented processes and procedures that define how your business operates and ensures consistency.
How It Works:
- Start by mapping out your existing workflows, from sales to delivery.
- Identify areas where documentation is missing or unclear.
- Use the ISO 9001 Guide to create policies that align with the standard, like quality objectives or guidelines for handling non-conformities.
For instance, a manufacturing company might document steps for quality checks at each stage of production, ensuring every product meets customer expectations.
4. Train Your Team
Your team plays a huge role in the success of your ISO 9001 implementation. Everyone needs to understand their responsibilities and how they contribute to maintaining quality.
How It Works:
Hold training sessions to explain the basics of ISO 9001 and how it impacts their daily tasks. Make it interactive—employees are more likely to embrace the changes if they feel involved and see the benefits.
5. Conduct Internal Audits
Before going for certification, it’s important to test your system with internal audits. These audits help you catch any issues and make improvements before the official evaluation.
How It Works:
Assign team members to review different parts of your QMS. For example, one person might review documentation while another evaluates how well processes are being followed. Use the findings to refine your system and address any gaps.
6. Schedule the Certification Audit
Once your QMS is ready, it’s time for the big day—the certification audit. This is where an external auditor assesses whether your business meets ISO 9001 standards.
How It Works:
Choose an accredited certification body and schedule your audit. Be sure to have all your documentation in order and your team prepared to answer questions about their roles. Passing this audit means your business is officially ISO 9001 certified!
7. Maintain and Improve
ISO 9001 isn’t a one-and-done deal—it’s a commitment to continuous improvement. After achieving certification, you’ll need to conduct regular audits, gather feedback, and refine your processes to stay compliant and competitive.
How It Works:
For example, a retail store might use monthly customer surveys to identify areas for improvement, such as shorter wait times at checkout. By addressing these issues, the business ensures it continues to meet ISO 9001 standards and keeps customers happy.
Why This Process Works
Implementing ISO 9001 might seem like a big project, but when you break it down into these manageable steps, it becomes much more achievable. This ISO 9001 Guide is here to remind you that every small step—whether it’s documenting a process or training your team—gets you closer to building a strong, quality-focused business.
In the next section, we’ll tackle common misconceptions about ISO 9001 that might be holding you back. Let’s clear the air and keep moving forward!
Benefits of Following This ISO 9001 Guide
By now, you’re probably wondering, “What’s in it for me if I follow this ISO 9001 Guide?” The answer is simple: implementing ISO 9001 can transform your business in ways you might not expect. Whether you’re aiming to improve customer satisfaction, streamline operations, or stand out in a crowded market, the benefits are worth the effort. Let’s break down how this guide to ISO 9001 can help you create a more efficient, competitive, and successful organization.
1. Deliver Consistent Quality
One of the most immediate benefits of ISO 9001 is that it helps you deliver consistent, high-quality products or services. When you follow the processes outlined in this ISO 9001 Guide, you’re setting up systems that ensure reliability and eliminate guesswork.
Example:
Imagine you’re running a bakery. By standardizing recipes, monitoring ingredient quality, and ensuring every team member follows the same procedures, you can guarantee that every cake or loaf of bread meets your customers’ expectations. That consistency builds trust and loyalty.
2. Improve Customer Satisfaction
Happy customers are the heart of any business, and ISO 9001 makes them a top priority. The standard emphasizes understanding customer needs, addressing complaints, and continually improving to exceed expectations.
Example:
Let’s say you run a small IT support company. By tracking customer feedback and using it to enhance your services, you can reduce response times and solve issues more effectively. This leads to happier clients who are more likely to recommend your business to others.
3. Boost Efficiency and Reduce Waste
Following the ISO 9001 Guide isn’t just about quality—it’s also about efficiency. By analyzing your workflows and eliminating unnecessary steps, you can save time, cut costs, and reduce waste.
Example:
A manufacturing company might find that by reorganizing their production line and introducing regular maintenance schedules, they can significantly reduce downtime and material waste. The result? Lower expenses and higher profits.
4. Build Credibility and Open New Doors
ISO 9001 certification is recognized worldwide, which means it’s a powerful way to show that your business is serious about quality. This can help you attract new clients, win bigger contracts, and even expand into international markets.
Example:
A small construction firm might use their ISO 9001 certification to bid on government projects that require proof of quality management systems. That certification sets them apart from competitors who haven’t taken the same step.
5. Foster a Culture of Continuous Improvement
ISO 9001 isn’t just about meeting today’s standards—it’s about staying ahead of the curve. When you follow this ISO 9001 Guide, you’re committing to regularly reviewing your processes and finding ways to make them even better.
Example:
A retail store might use sales data to identify peak shopping hours, then adjust staffing schedules to better serve customers during busy times. Small improvements like this add up and keep your business thriving.
6. Enhance Employee Engagement
Your team is one of your greatest assets, and ISO 9001 encourages you to involve them in creating and maintaining quality systems. When employees feel valued and understand their roles, they’re more likely to stay motivated and engaged.
Example:
A hotel that trains staff on ISO 9001 processes might see an improvement in service quality, as employees take pride in their work and feel empowered to deliver excellent experiences for guests.
Why It’s Worth It
The benefits of following this ISO 9001 Guide go beyond the technicalities of certification. It’s about building a business that operates efficiently, adapts to change, and consistently delivers value to customers. The effort you put into implementing ISO 9001 will pay off in increased trust, improved operations, and long-term success.
In the final section, we’ll tie everything together and encourage you to take the first steps toward mastering ISO 9001. Let’s wrap this up and get you started on your journey!
Conclusion: Start Your ISO 9001 Journey Today
By now, you’ve got a solid understanding of what ISO 9001 is, why it matters, and how to start implementing it. This ISO 9001 Guide has shown that adopting the standard isn’t just about earning a certificate—it’s about transforming your business from the inside out.
Whether you’re aiming to improve efficiency, enhance customer satisfaction, or stand out from competitors, ISO 9001 provides a clear roadmap to success. And the best part? It’s designed to be flexible, making it achievable for businesses of all sizes and industries.
Why ISO 9001 is Worth the Effort
Let’s recap some of the key benefits:
- Consistency: With ISO 9001, you’ll deliver high-quality products or services every time.
- Efficiency: Streamlined processes save time and money while reducing waste.
- Customer Trust: Certification shows customers you’re serious about meeting their expectations.
- Continuous Growth: The standard encourages ongoing improvement, keeping your business competitive.
By following this ISO 9001 Guide, you’re not just meeting a standard—you’re building a foundation for long-term success.
Your First Steps Toward ISO 9001
Taking the leap into ISO 9001 might feel like a big step, but remember, you don’t have to tackle it all at once. Here’s a simple plan to get started:
- Learn the Basics: Dive deeper into the standard’s requirements and how they apply to your business.
- Assess Your Current State: Conduct a gap analysis to see where you stand.
- Get Your Team Onboard: Share the vision with your employees and involve them in the process.
- Start Small: Focus on one area at a time, like improving documentation or streamlining a workflow.
Every small step brings you closer to creating a robust quality management system.
The Road Ahead
The journey to mastering ISO 9001 is an investment in your business’s future. It’s about creating a culture where quality, efficiency, and improvement are at the heart of everything you do. This ISO 9001 Guide is just the beginning—your path to greater success starts here.
So, what are you waiting for? Take that first step, start implementing the basics, and watch as your business grows stronger, more competitive, and better equipped to meet the challenges ahead. You’ve got this!
Looking for More Resources on ISO 9001?
Looking for ISO 9001 Resources Tailored to Your Industry?
If this article helped clarify ISO 9001, take the next step with our industry-focused tools designed to simplify your certification journey:
- ISO 9001 Documentation Kits by Industry: Whether you’re in manufacturing, construction, consulting, or healthcare — we have complete, ready-to-use documentation tailored for your sector.
- Online ISO 9001 Training: Learn how to implement ISO 9001 effectively with our easy-to-follow video lessons, real-world examples, and practical exercises.
- ISO 9001 Checklist: Download our step-by-step checklist to ensure your QMS meets all the 9001:2015 requirements from start to finish.
These resources are crafted to save you time, reduce stress, and help you achieve certification with confidence. Choose your industry and start now!
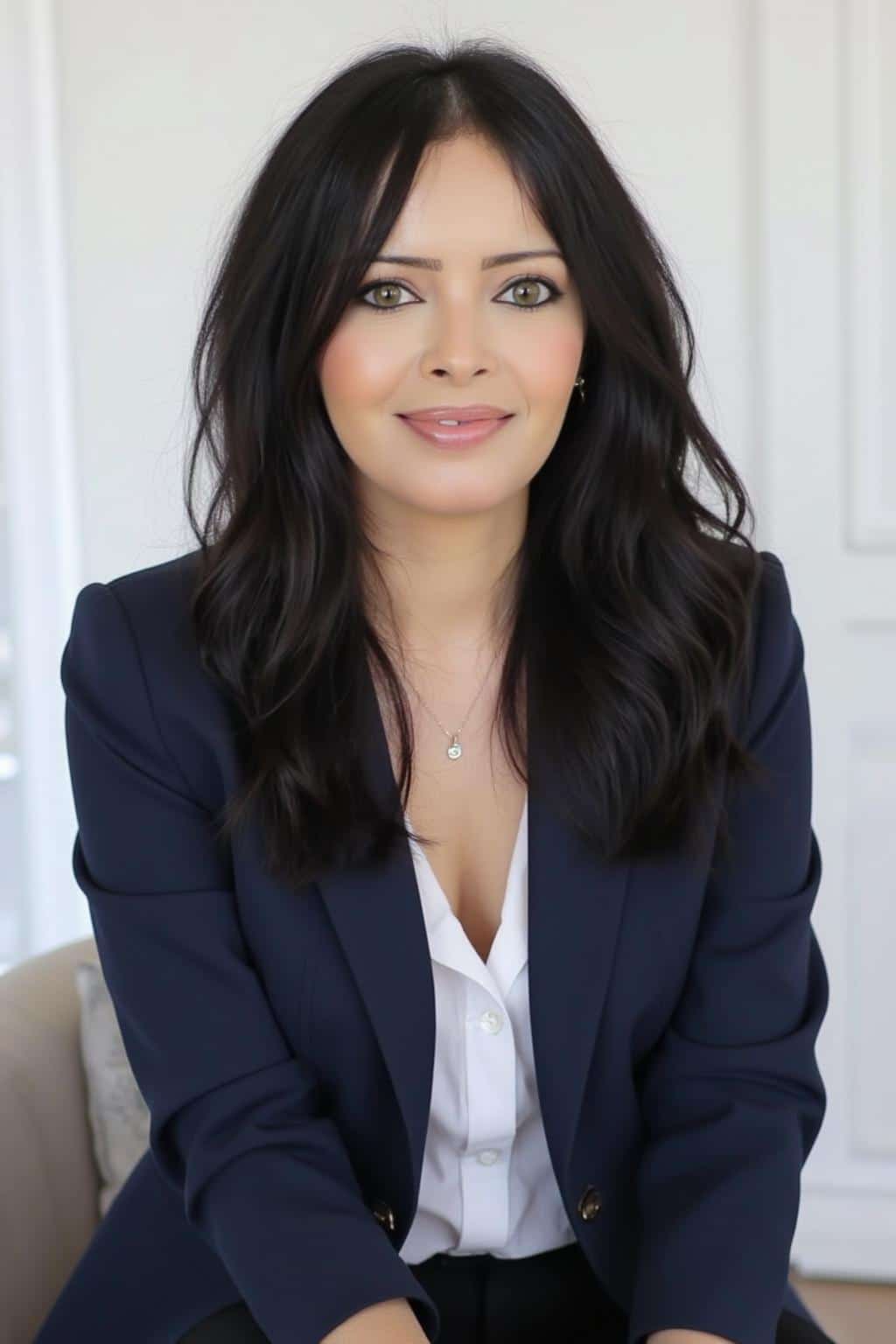
👋 Hi, I’m HAFSA, and for the past 12 years, I’ve been on a journey to
make ISO standards less intimidating and more approachable for everyone.
Whether it’s ISO 9001, ISO 22000, or the cosmetics-focused ISO 22716,
I’ve spent my career turning complex jargon into clear, actionable steps
that businesses can actually use. I’m not here to call myself an expert—I prefer “enthusiast” because I truly love what I do.
There’s something incredibly rewarding about helping people navigate food safety and quality management systems
in a way that feels simple, practical, and even enjoyable.
When I’m not writing about standards, you’ll probably find me playing Piano 🎹, connecting with people, or diving into my next big project💫.
I’m an engineer specialized in the food and agricultural industry
I have a Master’s in QHSE management and over 12 years of experience as a Quality Manager
I’ve helped more than 15 companies implement ISO 9001, ISO 22000, ISO 22716, GMP, and other standards
My clients include food producers, cosmetics manufacturers, laboratories, and service companies
I believe quality systems should be simple, useful, and efficient
Outside of work, I play piano and love learning something new every day
Let’s make ISO less about stress and more about success! 🙏