ISO 9001 2015 Requirements (Part 2)
ISO 9001 2015 Requirements (Part 2
If there’s one thing we can agree on, it’s that no system—no matter how well-designed—can succeed without the right support. That’s exactly why the ISO 9001 2015 Requirements dedicate an entire section to ensuring your organization has the resources, skills, and tools needed to bring your quality management system (QMS) to life. Let’s break down the “Support” clause step by step so it feels approachable and actionable.
1. Resources: Laying the Groundwork
Imagine trying to build a house without the proper tools or materials—it wouldn’t work, right? The same goes for your QMS. The ISO 9001 2015 Requirements stress the importance of ensuring your organization has adequate resources, whether it’s people, infrastructure, or technology.
Key Areas to Focus On:
- People: Do you have enough staff to handle the workload? Are they trained and equipped for their roles?
- Infrastructure: Think about your facilities, equipment, and technology—are they up to the task?
- Environment: This includes everything from workplace safety to maintaining a positive culture that supports quality objectives.
Example:
A manufacturing company might invest in modern machinery to improve product consistency and set up a well-ventilated production floor to ensure a safe working environment.
2. Competence and Training: Building Skills That Matter
One of the most important aspects of the ISO 9001 2015 Requirements is ensuring that your team is competent. This doesn’t just mean hiring skilled workers—it also means providing ongoing training and support to help them grow and succeed.
How to Ensure Competence:
- Identify the skills required for each role within your QMS.
- Provide regular training sessions to keep employees up to date on industry standards and company processes.
- Evaluate staff performance to identify any gaps and address them proactively.
Example:
An IT company might provide regular cybersecurity training to its team to ensure they’re equipped to handle the latest threats, aligning with both customer expectations and regulatory standards.
3. Communication: Keeping Everyone Aligned
Effective communication is the glue that holds your QMS together. The ISO 9001 2015 Requirements emphasize the need for clear and consistent communication—both internally and externally.
What to Communicate:
- Internally: Share updates on quality objectives, new processes, and performance metrics with your team.
- Externally: Keep customers, suppliers, and other stakeholders informed about changes or expectations.
Example:
A retail business might hold weekly team meetings to discuss sales performance and upcoming promotions, ensuring everyone is aligned on goals.
4. Documented Information: Staying Organized
Documentation is a big part of the ISO 9001 2015 Requirements, but don’t worry—it doesn’t have to be complicated. The key is to create and manage documents that are clear, relevant, and easy to access.
What to Document:
- Policies, procedures, and work instructions.
- Records of performance metrics, audits, and corrective actions.
- Evidence of training and competence.
Example:
A logistics company might use a digital system to store and update delivery procedures, making it easy for drivers and supervisors to access the latest information.
Why Support Matters
Support is the foundation that allows the rest of your QMS to thrive. Without adequate resources, trained employees, clear communication, and well-organized documentation, it’s nearly impossible to meet the ISO 9001 2015 Requirements. But when you get this right, everything else falls into place.
In the next section, we’ll explore the operations clause, diving into how to plan and control processes to consistently meet customer expectations. Stay tuned—it’s all about turning support into action!
Operations: Turning Plans into Action with ISO 9001 2015 Requirements
Now that we’ve tackled the foundation of support, let’s move on to the heart of the ISO 9001 2015 Requirements: operations. This section is where the rubber meets the road. It’s all about putting your plans into action to deliver consistent, high-quality products or services that meet customer expectations. Let’s break it down so it feels approachable and actionable.
1. Operational Planning and Control
Think of operational planning as your game plan for ensuring quality at every step of your process. The ISO 9001 2015 Requirements emphasize the importance of planning out your operations to make sure everything runs smoothly and efficiently.
How to Approach This:
- Clearly define your processes, from start to finish.
- Identify the resources needed for each step, including people, materials, and technology.
- Monitor and control each stage to ensure quality isn’t compromised.
Example:
A catering business might plan its operations by outlining steps for menu creation, ingredient sourcing, food preparation, and delivery, ensuring every stage meets customer expectations.
2. Understanding Customer Requirements
Meeting customer needs is at the core of the ISO 9001 2015 Requirements, and this starts with understanding exactly what your customers want. This includes identifying their stated requirements (like specific product features) and their implied needs (like reliability and timely delivery).
Steps to Meet Customer Requirements:
- Gather feedback through surveys or direct conversations.
- Clearly document customer requirements and expectations.
- Monitor your processes to ensure you consistently meet these needs.
Example:
An online retailer might implement a system to track customer preferences and ensure their shipping times align with customer expectations for quick delivery.
3. Design and Development
For businesses that create new products or services, the design and development process is a critical part of the ISO 9001 2015 Requirements. This clause ensures that what you’re creating is aligned with customer needs, regulatory requirements, and your quality objectives.
Key Steps in Design and Development:
- Plan out the design process, including timelines and resources.
- Review and test prototypes or initial concepts.
- Gather input from stakeholders to refine the final product or service.
Example:
A tech company developing a new app might involve customers in the beta testing phase to ensure the final product meets user expectations.
4. Managing External Providers
Many businesses rely on suppliers or third-party providers to deliver their products or services. The ISO 9001 2015 Requirements highlight the importance of controlling these external processes to ensure they align with your quality standards.
How to Manage External Providers:
- Clearly define quality expectations in contracts or agreements.
- Regularly evaluate supplier performance.
- Maintain open communication to address any issues quickly.
Example:
A clothing brand might work closely with fabric suppliers to ensure consistent quality and timely deliveries, conducting periodic reviews to maintain standards.
5. Delivering Products and Services
The final step in operations is delivering your product or service to the customer. This might sound simple, but the ISO 9001 2015 Requirements emphasize the importance of maintaining quality during this stage to ensure customer satisfaction.
Best Practices for Delivery:
- Monitor production or service delivery to identify and fix issues in real time.
- Ensure packaging, labeling, and presentation meet customer expectations.
- Gather feedback after delivery to identify areas for improvement.
Example:
A pharmaceutical company might use strict quality controls during packaging and shipping to ensure products reach customers in perfect condition.
Why Operations Matter
Operations are where all the planning, support, and leadership come together to create real results. By following the ISO 9001 2015 Requirements for operations, you’re not just meeting standards—you’re building trust with your customers and ensuring your business runs smoothly.
In the next section, we’ll explore how to evaluate your performance through monitoring, measurement, and internal audits. It’s all about making sure your hard work pays off and identifying opportunities for improvement. Let’s keep building!
Performance Evaluation: Measuring Success with ISO 9001 2015 Requirements
Now that your operations are in full swing, how do you know if your quality management system (QMS) is actually working? That’s where performance evaluation comes in. The ISO 9001 2015 Requirements emphasize the importance of monitoring, measuring, and evaluating your processes to ensure they’re delivering the results you want—and to identify areas for improvement.
Let’s break this down so you can measure your success without feeling overwhelmed.
1. Monitoring and Measurement
You can’t improve what you don’t measure, right? The ISO 9001 2015 Requirements encourage organizations to track key metrics that reflect the performance of their QMS. Monitoring and measurement allow you to spot trends, identify issues, and take corrective action before small problems turn into big ones.
How to Approach Monitoring and Measurement:
- Identify key performance indicators (KPIs) that align with your quality objectives.
- Use tools like surveys, audits, and data analysis to collect information.
- Regularly review your results to track progress and adjust as needed.
Example:
A customer service center might measure response times, customer satisfaction scores, and resolution rates to ensure they’re meeting service-level agreements (SLAs).
2. Internal Audits: A Reality Check for Your QMS
Internal audits are like a health check for your QMS. They give you a chance to see how well your processes align with the ISO 9001 2015 Requirements and identify any gaps.
How to Conduct Effective Internal Audits:
- Develop a schedule for regular audits.
- Focus on high-risk areas or processes that directly impact quality.
- Ensure objectivity by having someone independent of the process perform the audit.
Example:
A manufacturing company might conduct internal audits to review compliance with safety protocols and check whether production timelines are being met without sacrificing quality.
3. Management Review: The Bigger Picture
While monitoring and internal audits focus on the details, management reviews take a step back to look at the big picture. The ISO 9001 2015 Requirements call for regular reviews by top management to evaluate the overall effectiveness of the QMS.
What to Cover in a Management Review:
- Performance data, including KPIs and audit findings.
- Feedback from customers and other stakeholders.
- Progress toward quality objectives and areas for improvement.
Example:
A retail chain’s management team might review sales data, customer complaints, and supplier performance to identify trends and adjust their strategy for the upcoming quarter.
Why Performance Evaluation Matters
Performance evaluation isn’t just about meeting the ISO 9001 2015 Requirements—it’s about ensuring your QMS delivers real value to your organization. By monitoring, measuring, and reviewing your processes, you can:
- Continuously improve and adapt to changing conditions.
- Build trust with stakeholders by showing them the results of your efforts.
- Ensure long-term success by staying proactive rather than reactive.
In the next section, we’ll dive into the final piece of the puzzle: continual improvement. It’s all about taking what you’ve learned from performance evaluation and using it to make your QMS even better. Let’s keep going—you’re almost there!
Continual Improvement: The Heart of ISO 9001 2015 Requirements
Congratulations! By now, you’ve built a solid quality management system (QMS) following the ISO 9001 2015 Requirements. But here’s the thing: achieving certification isn’t the end—it’s just the beginning. Continual improvement is at the core of ISO 9001, ensuring your business doesn’t just maintain its standards but gets better over time.
Let’s dive into how you can embrace the spirit of continual improvement and make it a natural part of your operations.
1. Nonconformity and Corrective Action
Let’s face it—no system is perfect, and mistakes happen. The ISO 9001 2015 Requirements recognize this and emphasize the importance of addressing nonconformities when they occur. A nonconformity could be anything that doesn’t meet your standards or your customers’ expectations.
How to Handle Nonconformities:
- Identify the Issue: Determine what went wrong and why.
- Take Corrective Action: Address the root cause of the problem, not just the symptoms.
- Prevent Recurrence: Put measures in place to ensure the issue doesn’t happen again.
Example:
A logistics company might find that a spike in late deliveries was caused by outdated routing software. To fix this, they upgrade the software and train drivers on the new system, reducing delays moving forward.
2. Learning from Feedback
Feedback is a goldmine for improvement opportunities. Whether it comes from customers, employees, or suppliers, the insights you gain can help you fine-tune your processes to better meet the ISO 9001 2015 Requirements.
Sources of Feedback:
- Customer Feedback: Use surveys, reviews, and complaints to understand what’s working and what’s not.
- Employee Input: Encourage your team to share ideas for improvement—they’re often the ones who see inefficiencies firsthand.
- Supplier Collaboration: Work with your suppliers to identify ways to improve quality and streamline processes.
Example:
A restaurant chain might act on customer feedback about long wait times by streamlining kitchen processes and introducing a table management system.
3. Embracing Innovation
Improvement isn’t just about fixing what’s broken—it’s also about finding new ways to do things better. The ISO 9001 2015 Requirements encourage businesses to look for innovative solutions that enhance quality and efficiency.
Ways to Foster Innovation:
- Stay updated on industry trends and best practices.
- Use technology to automate repetitive tasks and reduce errors.
- Encourage brainstorming sessions with your team to spark fresh ideas.
Example:
A small software company might adopt artificial intelligence tools to improve the speed and accuracy of their code testing processes, leading to faster product launches.
4. Regular Reviews and Updates
Improvement doesn’t happen by chance—it requires regular reviews to identify what’s working and what needs adjustment. The ISO 9001 2015 Requirements recommend using performance data, audit results, and feedback to guide your improvement efforts.
What to Review:
- Are you meeting your quality objectives?
- Are there recurring issues or bottlenecks in your processes?
- Are you taking advantage of opportunities to innovate or improve?
Example:
A healthcare provider might review patient satisfaction scores quarterly and adjust its appointment booking process to make it more user-friendly.
Why Continual Improvement Matters
Continual improvement isn’t just about meeting the ISO 9001 2015 Requirements—it’s about staying ahead in a competitive market. When improvement becomes a core part of your business culture, you’ll:
- Build stronger relationships with customers by consistently exceeding their expectations.
- Empower your team by involving them in the process of making things better.
- Ensure your business remains adaptable, efficient, and future-proof.
In wrapping up Part 2 of the ISO 9001 2015 Requirements, you’ve learned how to take your QMS from good to great. By focusing on continual improvement, you’re setting the stage for long-term success. In the next installment, we’ll explore real-world examples and practical tips to help you bring everything together. Let’s keep pushing forward—you’re doing amazing!
Practical Tips for Success with ISO 9001 2015 Requirements
So far, we’ve walked through the key clauses of the ISO 9001 2015 Requirements, from leadership to operations and continual improvement. Now it’s time to talk about how you can take everything you’ve learned and turn it into action. The good news? Success with ISO 9001 isn’t about perfection—it’s about consistent progress. Here are some practical tips to help you implement the requirements and see real results.
1. Break It Down into Manageable Steps
The ISO 9001 2015 Requirements can feel overwhelming if you try to tackle everything at once. Instead, break it down into smaller, actionable steps.
How to Do This:
- Start by conducting a gap analysis to identify areas where your current processes fall short.
- Prioritize one section or clause at a time—focus on addressing the biggest gaps first.
- Set realistic timelines for each step, so you don’t feel rushed.
Example:
If your documentation is outdated, start by revising your quality policy and procedures. Once that’s done, move on to areas like internal audits or training programs.
2. Use Templates and Tools
You don’t have to start from scratch when implementing the ISO 9001 2015 Requirements. There are plenty of templates, guides, and software tools available to simplify the process.
What to Look For:
- Document templates for policies, procedures, and work instructions.
- Quality management software to track performance metrics and manage audits.
- Checklists to ensure you’ve covered all the necessary requirements.
Example:
A small consultancy firm might use a pre-built audit checklist to streamline internal reviews and ensure compliance without wasting time on unnecessary paperwork.
3. Involve Your Team
Remember, ISO 9001 isn’t just a top-down initiative—it’s a team effort. Engaging your employees not only lightens the workload but also builds a culture of quality throughout your organization.
How to Involve Your Team:
- Hold regular meetings to explain the ISO 9001 2015 Requirements and their importance.
- Assign specific roles and responsibilities to team members based on their expertise.
- Encourage employees to share feedback and ideas for improvement.
Example:
A manufacturing plant might form a cross-departmental quality team to tackle nonconformities and brainstorm ways to improve processes.
4. Focus on Continuous Improvement
The ISO 9001 2015 Requirements are built around the idea of continual improvement. Make this a central part of your implementation strategy to keep your QMS dynamic and effective.
Ways to Foster Continuous Improvement:
- Use customer feedback to identify areas for enhancement.
- Conduct regular internal audits to uncover opportunities for growth.
- Celebrate small wins to keep your team motivated and engaged.
Example:
An e-commerce company might analyze customer complaints about delivery delays and adjust its logistics process to improve shipping times.
5. Regularly Review and Adjust
Meeting the ISO 9001 2015 Requirements isn’t a one-time effort—it’s an ongoing process. Regularly reviewing your QMS helps you adapt to changes, improve performance, and stay compliant.
What to Review:
- Key performance indicators (KPIs) to track progress toward quality objectives.
- Feedback from customers, employees, and suppliers.
- Results from internal and external audits.
Example:
A healthcare clinic might review its patient satisfaction scores every quarter to ensure it’s meeting quality objectives and making necessary adjustments.
Why These Tips Matter
Successfully implementing the ISO 9001 2015 Requirements doesn’t have to be complicated. By breaking it down into smaller steps, leveraging the right tools, and involving your team, you can create a QMS that’s not only compliant but also drives meaningful improvements in your business.
In the final section, we’ll wrap up this journey by reflecting on how ISO 9001 can transform your organization and set you on the path to long-term success. You’re almost there—let’s bring it all together!
Conclusion: How ISO 9001 2015 Requirements Can Transform Your Business
We’ve covered a lot of ground in this guide, from leadership and operations to performance evaluation and continual improvement. By now, you can probably see how the ISO 9001 2015 Requirements provide more than just a framework for certification—they offer a blueprint for long-term success.
Whether you’re aiming to improve efficiency, boost customer satisfaction, or simply streamline your processes, ISO 9001 helps you achieve all that and more. Let’s reflect on how these requirements can make a lasting impact on your business.
Why ISO 9001 2015 Requirements Matter
At its core, the ISO 9001 2015 Requirements are about creating a quality management system (QMS) that works for you. It’s not a rigid set of rules—it’s a flexible guide that you can adapt to your specific needs.
By implementing ISO 9001, you:
- Build trust with customers through consistent quality.
- Empower your team with clear roles, responsibilities, and opportunities for growth.
- Stay proactive by addressing risks and leveraging opportunities.
- Create a culture of continuous improvement that keeps your business moving forward.
Example:
Imagine a small marketing agency. By following the ISO 9001 2015 Requirements, they streamline project management, improve client communication, and reduce errors in campaign delivery. As a result, they attract more clients and foster long-term partnerships.
Making ISO 9001 a Part of Your Business DNA
The beauty of the ISO 9001 2015 Requirements is that they’re not just about achieving certification—they’re about embedding quality into every aspect of your business. When you make ISO 9001 a part of your daily operations, it becomes second nature.
How to Make It Stick:
- Involve your team: Quality shouldn’t be a one-person job. Get everyone on board and make it a shared responsibility.
- Keep improving: Use audits, reviews, and feedback to identify ways to evolve and grow.
- Celebrate progress: Acknowledge milestones and improvements to keep your team motivated.
Your Next Steps
So, where do you go from here? Here’s a quick checklist to get started:
- Review the key clauses of the ISO 9001 2015 Requirements and assess your current processes.
- Prioritize areas for improvement and start making small, consistent changes.
- Seek support if needed—whether it’s consulting with an expert or using tools and templates.
- Remember, this is a journey, not a race. Take it one step at a time, and you’ll see the results.
Final Thoughts
Implementing the ISO 9001 2015 Requirements is a smart investment in your business’s future. It’s not just about compliance—it’s about building a stronger, more efficient, and more resilient organization.
So take the first step today. Whether you’re just starting or refining an existing QMS, every improvement brings you closer to your goals. And remember, this is your journey—you’ve got the tools and knowledge to make it a success. Let’s keep moving forward together!
Looking for More Resources on ISO 9001?
Looking for ISO 9001 Resources Tailored to Your Industry?
If this article helped clarify ISO 9001, take the next step with our industry-focused tools designed to simplify your certification journey:
📦 ISO 9001 Documentation Kits by Industry: Whether you’re in manufacturing, construction, consulting, or healthcare — we have complete, ready-to-use documentation tailored for your sector.
🎓 Online ISO 9001 Training: Learn how to implement ISO 9001 effectively with our easy-to-follow video lessons, real-world examples, and practical exercises.
📋 ISO 9001 Checklist: Download our step-by-step checklist to ensure your QMS meets all the 9001:2015 requirements from start to finish.
These resources are crafted to save you time, reduce stress, and help you achieve certification with confidence. Choose your industry and start now!
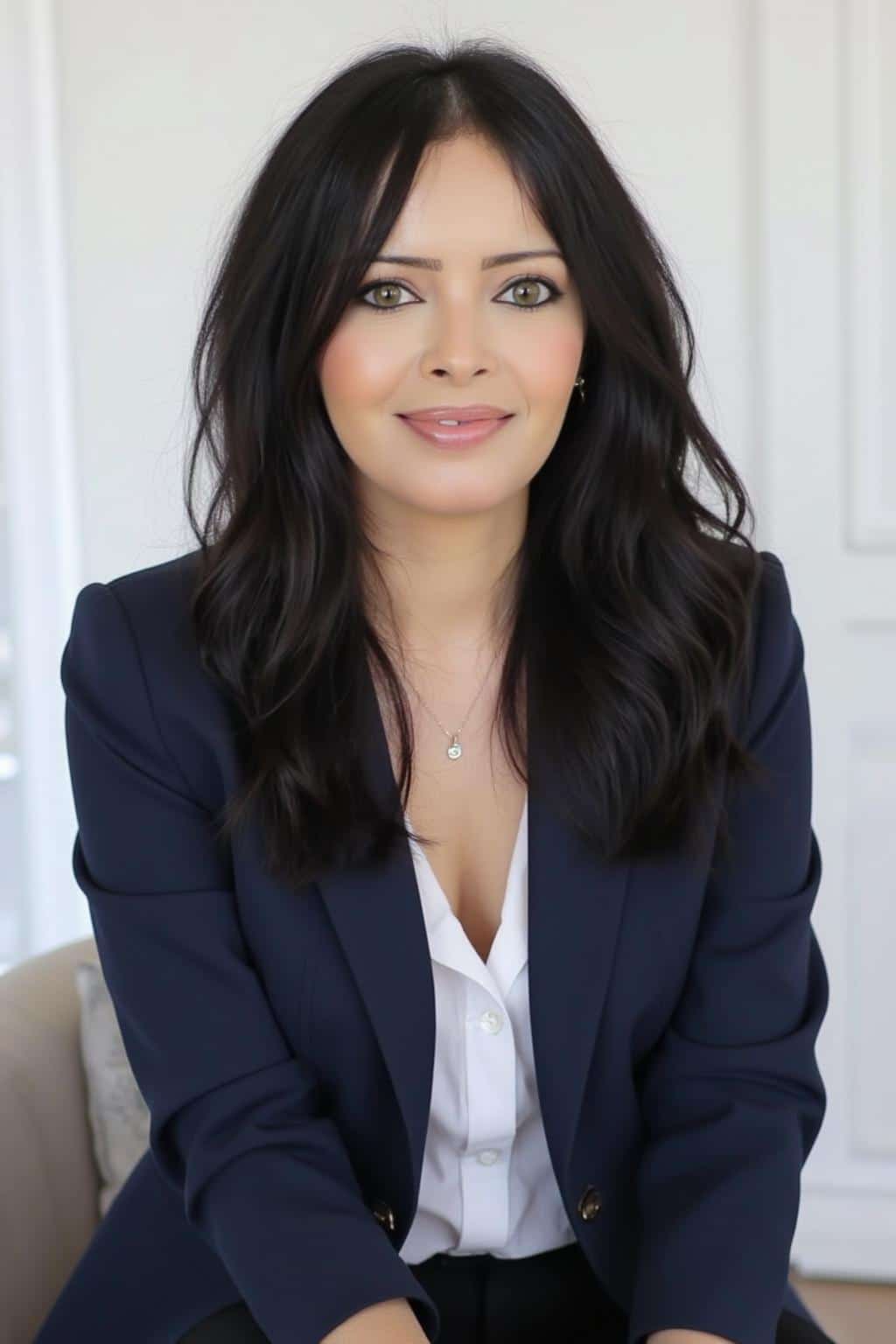
👋 Hi, I’m HAFSA, and for the past 12 years, I’ve been on a journey to
make ISO standards less intimidating and more approachable for everyone.
Whether it’s ISO 9001, ISO 22000, or the cosmetics-focused ISO 22716,
I’ve spent my career turning complex jargon into clear, actionable steps
that businesses can actually use. I’m not here to call myself an expert—I prefer “enthusiast” because I truly love what I do.
There’s something incredibly rewarding about helping people navigate food safety and quality management systems
in a way that feels simple, practical, and even enjoyable.
When I’m not writing about standards, you’ll probably find me playing Piano 🎹, connecting with people, or diving into my next big project💫.
I’m an engineer specialized in the food and agricultural industry
I have a Master’s in QHSE management and over 12 years of experience as a Quality Manager
I’ve helped more than 15 companies implement ISO 9001, ISO 22000, ISO 22716, GMP, and other standards
My clients include food producers, cosmetics manufacturers, laboratories, and service companies
I believe quality systems should be simple, useful, and efficient
Outside of work, I play piano and love learning something new every day
Let’s make ISO less about stress and more about success! 🙏